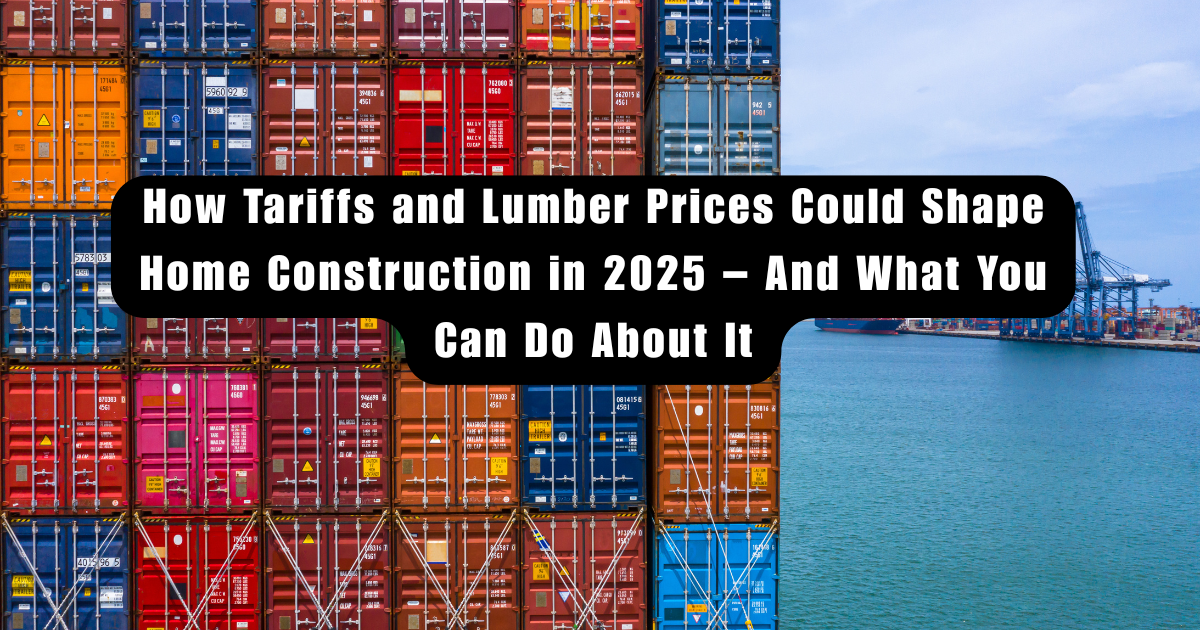
How Tariffs and Lumber Prices Could Shape Home Construction in 2025 – And What You Can Do About It
As we head into the second half of 2025, the home construction landscape is shifting under the weight of rising costs, fluctuating material prices, and evolving regulatory challenges. One major factor set to impact the industry is the looming increase in U.S. tariffs on Canadian softwood lumber.
Why Tariffs Matter for Home Construction
The National Association of Home Builders estimates new home construction costs will rise by $10,900 on average as a result of tariffs. Tariffs will affect everything from softwood lumber and rebar from Canada to appliances from China.
Recent data shows that while lumber futures have eased slightly to around $610 per thousand board feet—down from a three-month high of $627 at the end of June—the North American housing market remains in a state of flux. A cooling market, higher mortgage rates, and sagging builder sentiment have caused a shift toward “just-in-time” material purchasing. Builders are increasingly wary of taking on inventory at inflated prices, especially with trade policy uncertainties looming large.
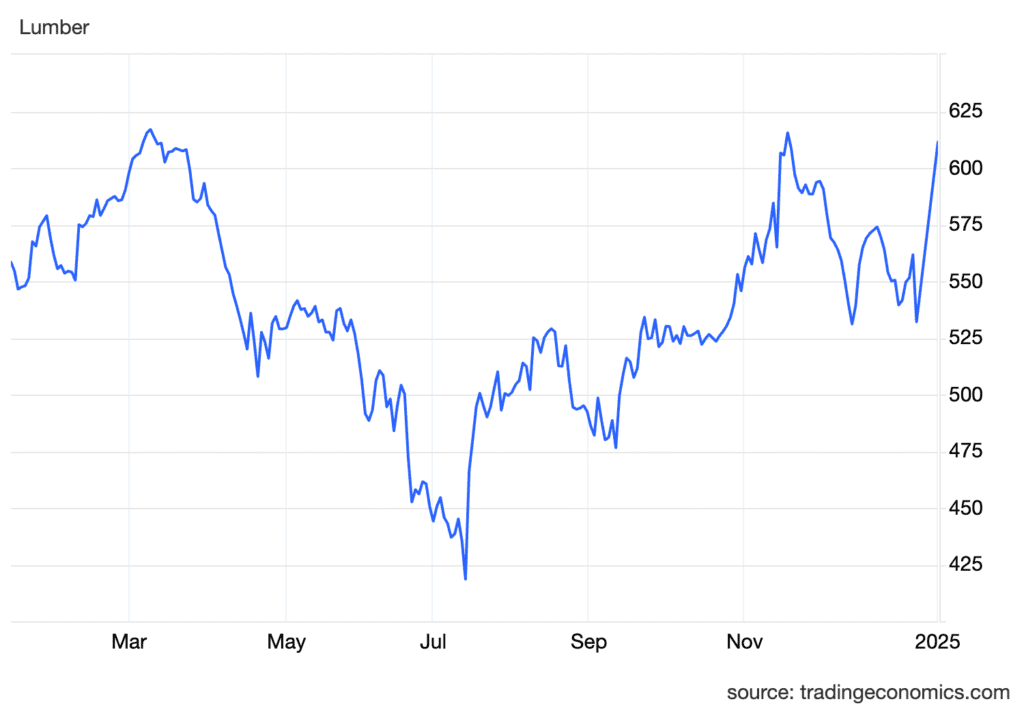
In particular, U.S. tariffs on Canadian softwood lumber are creating hesitancy in the market. The U.S. imports a significant portion of its lumber from Canada, and tariffs can cause price volatility, supply disruptions, and ultimately, higher construction costs.
Despite a slowdown in demand, production cuts at smaller Eastern mills, log shortages due to severe weather in the Southeast, and consistent export demand from Asia have tightened availability of certain specialty and dimension grades. The result? A market that is unpredictable, but still pricey.
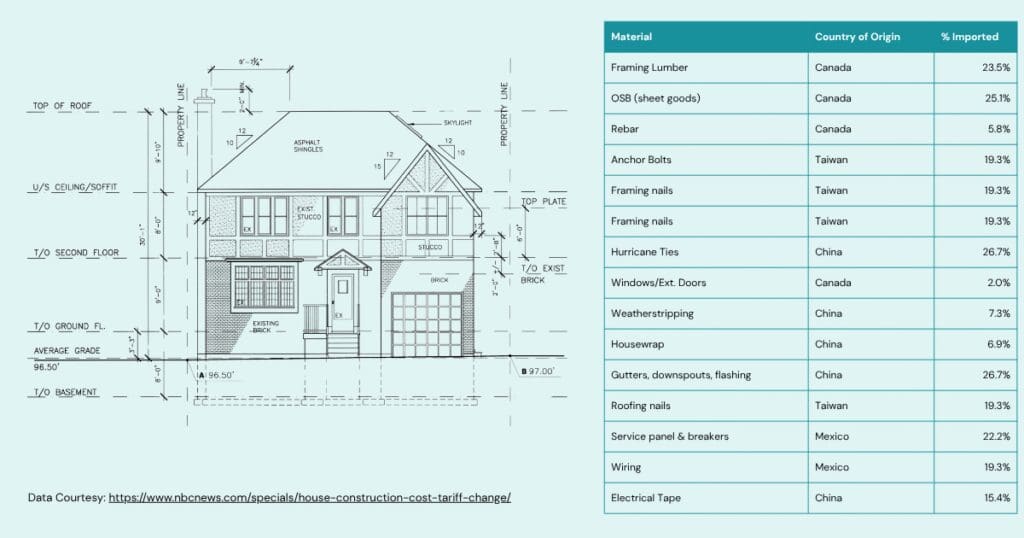
Smart Cost-Saving Strategies for 2025 Builds
At Casper Builders, we’re committed to helping homeowners navigate these challenges while keeping projects on time and on budget. Here are a few ways you can adapt your building plans to stay ahead:
1. Simplify the Home’s Footprint and Roof Design
Complex rooflines and elaborate foundations can add tens of thousands of dollars to your build. Opting for a more straightforward layout can significantly reduce material and labor costs, especially as those costs rise unpredictably.
2. Consider Insulated Concrete Forms (ICFs)
ICF homes may have historically been more expensive than traditional wood framing due to the cost of concrete, but with the U.S. importing less concrete than lumber—and tariffs unlikely to affect concrete to the same degree—they’re becoming an attractive, durable alternative. Bonus: they offer excellent energy efficiency and many ICF homeowners find their insurance rates are lower!
3. Use Standard Sizes and Stock Materials
Custom dimensions often come with long lead times and inflated prices. Choosing standard materials and sizes not only keeps costs down but also reduces the risk of delays caused by specialty orders or tariff-driven shortages.
4. Smaller Can Be Smarter
Rather than building the largest house your budget allows, consider focusing on well-designed, functional spaces. Strategic downsizing not only saves money but can result in a more efficient, comfortable home.
Prepare Now for a Smarter Build Later
The construction landscape in 2025 will require flexibility, creativity, and foresight. By working with a builder who understands the complexities of today’s market and knows how to navigate fluctuating prices and tariffs, you can build the home of your dreams without breaking the bank.
Ready to get started? Contact us today to discuss your home construction plans and learn how we can help you design smart and build strong in 2025.